Ultrasonic Inspection of Composites
The extensive use of glass and carbon fiber composites in manufacturing of modern aerospace components is raising the need for reliable, cost-effective NDT systems for the ultrasonic inspection of such components in the manufacturing stage.
The complexity of the new multilayered parts of complicated geometry with high curvatures and varying thicknesses and the requirement to inspect the parts on a 100% rate are posing serious challenges to such systems.
For example, stringer webs, flanges, edges, radii and chamfers as well as untrimmed part and parts drilled with holes must be completely inspected.
Ultrasonic Inspection of Composites: System Gallery
Supported Scanner Configurations
Travelling bridge type scanners
suitable for inspection of single curvature parts (one bridge systems) or double curvature parts (two bridge systems). This configuration requires minimal floor space and permits use of a turntable for high throughput inspection of round structures. A removable immersion tank can be provided as required.
Dual tower scanners
appropriate for scanning complex double curvature parts. A removable immersion tank can also be provided in this configuration.
Flatbed systems
used for inspection of flat parts or parts of moderate curvature. These scanners of ultrasonic inspection of composites, are usually equipped with multiple squirters for productivity enhancement.
Parts of complex shape can also be inspected by squirter systems using industrial robots.
Features and Benefits
- Fully integrated systems: All system components are designed, manufactured and tested by ScanMaster, ensuring smooth, reliable operation of the system as a whole
- Scanning speeds of up to 1,000 mm/second
- Simultaneous inspection in through transmission and pulse echo modes
- Simultaneous inspection with linear and logarithmic amplifiers
- Dual squirter, dual frequency features for high throughput
- Easy part programming through intuitive Teach In tools, including import of CAD files such as CATIA
- Advanced image analysis and processing tools
- Adherence to Airbus and Boeing requirements
- Packaged water systems with active flaw control, including storage, filtration and UV treatment
- Optional turntable and part fixtures
- Optional removable immersion tank (gantry and dual tower configurations)
LS-200 COPA
Phased Array Immersion Scanner for Automatic Ultrasonic Inspection of Composite Panels, Skins and Stringer Components
The extensive use of glass and carbon fiber composites in manufacturing of modern aerospace components is raising the need for reliable, cost-effective NDT systems for the inspection of such components in the manufacturing stage. The complexity of the new multilayered parts of complicated geometry with high curvatures and varying thicknesses and the requirement to inspect the parts on a 100% rate are posing serious challenges to such systems. For example, stringer webs, flanges, edges, radii and chamfers as well as untrimmed part and parts drilled with holes must be completely inspected.
ScanMaster LS-200-COPA immersion scanners provide an efficient, automated solution for the ultrasonic inspection of Carbon and Glass-Fiber-Reinforced Polymer parts, such as skins, stringers, and spars. The
inspection is making use of multi-channel ultrasonic phased array (PA) technology, which is well proven for such applications.
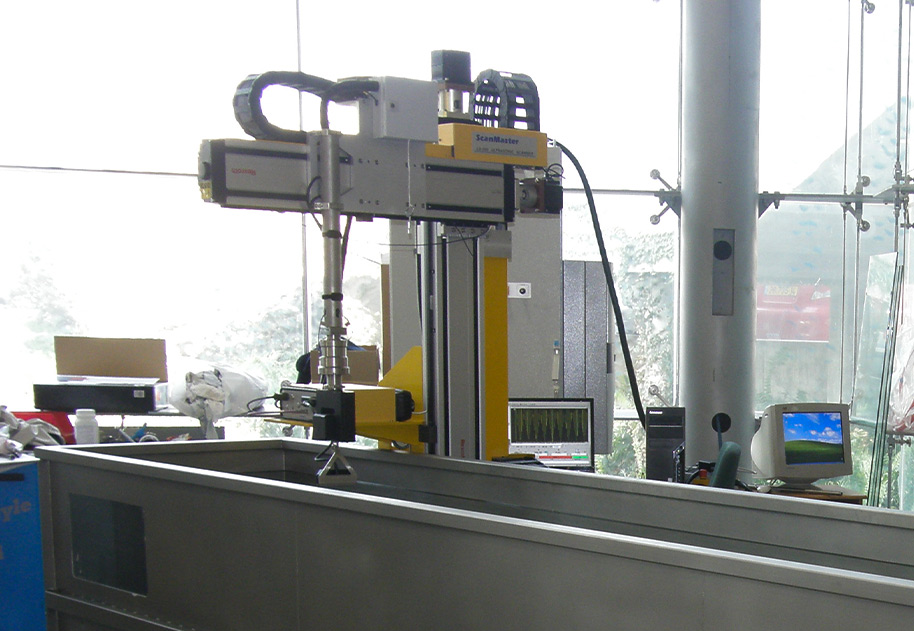
What is water jet ultrasonic inspection?
Water jet (squirters) ultrasonic inspection is a cutting-edge technique utilized for the meticulous examination of composite materials. Particularly suitable for dense materials and those with significant sound dissipation properties, such as glass fiber composites, this method has become the industry standard for inspecting such composites. By employing water jets coupled with ultrasonic waves, this non-destructive testing approach allows for thorough through-transmission inspection. It is highly effective in detecting internal defects, delaminations, and anomalies that may compromise the structural integrity of composite materials. Whether it's examining buoyant composites or components vulnerable to water ingress, water jet ultrasonic inspection provides unparalleled accuracy and reliability, ensuring the highest quality and safety standards in various industries, mainly for aerospace manufacturing.